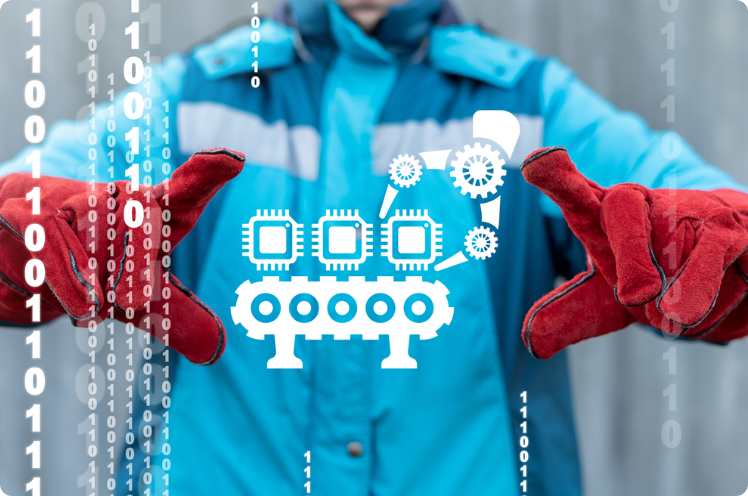
Unlocking Efficiency and Quality: The Impact of AI in PCB Assembly
The electronics industry has always been a rapidly evolving field, but the integration of artificial intelligence (AI) has emerged as a game-changer in the realm of PCB (Printed Circuit Board) assembly. From optimizing production processes to automating and enhancing quality control, AI is revolutionizing every aspect of PCB assembly. This transformative technology leverages advanced algorithms and machine learning techniques to drive efficiency, accuracy, and innovation across the assembly line. By precisely placing components, diagnosing faults, predicting maintenance needs, and optimizing workflows, AI is unlocking new levels of productivity and competitiveness for manufacturers. In this article, we dive into the multiple roles that AI plays in printed circuit board assembly.
Predictive Maintenance
AI algorithms are capable of analyzing historical equipment data to anticipate maintenance needs. By spotting patterns, AI predicts when equipment might fail, allowing proactive maintenance scheduling to minimize downtime. This improves efficiency and reduces disruptions in the assembly process.
Furthermore, AI-powered predictive maintenance systems can prioritize maintenance tasks based on the severity of the predicted issues, ensuring that resources are allocated efficiently. For example, critical equipment might receive immediate attention, while less critical components can be scheduled for maintenance at a later time.
Process Optimization
Process optimization in PCB assembly involves using AI to analyze and improve various aspects of the assembly process to enhance efficiency, quality, and cost-effectiveness. Here’s how AI can optimize PCB assembly processes:
• Parameter Optimization: AI algorithms analyze data from the assembly process, such as soldering temperature, conveyor speed, and component placement accuracy, to identify optimal parameter settings. By adjusting these parameters based on real-time feedback and historical data, AI ensures that the assembly process operates at peak efficiency while maintaining quality standards.
• Material Management: AI optimizes material usage and inventory management by analyzing production data and demand forecasts. By ensuring the availability of the right components at the right time, AI minimizes delays and bottlenecks in the assembly process.
• Production Scheduling: AI algorithms optimize production schedules by considering factors such as equipment availability, order priority, and resource constraints. By dynamically adjusting schedules in response to changing conditions, AI maximizes throughput and minimizes lead times.
• Energy Efficiency: AI analyzes energy consumption data to identify opportunities for reducing energy usage and optimizing equipment operation. By minimizing energy waste and optimizing resource utilization, AI helps reduce operating costs and environmental impact.
• Workflow Automation: AI automates repetitive tasks and workflows, such as data entry, documentation, and reporting, to streamline the assembly process. By eliminating manual tasks and reducing human error, AI improves efficiency and accuracy while freeing up resources for higher-value activities.
Robotic Assembly
Robotic arms equipped with AI algorithms precisely pick and place components onto the PCB according to the optimized layout determined by the AI. These robotic arms are capable of high-speed and high-precision movements, allowing for rapid and accurate assembly of printed circuit boards. While more traditional SMT pick and place machines are extremely efficient to place SMD components, robotic arms present advantages under certain situations. For example, thanks to their higher number of degrees of freedom, robot arms are well suited to place both SMD and through-hole components.
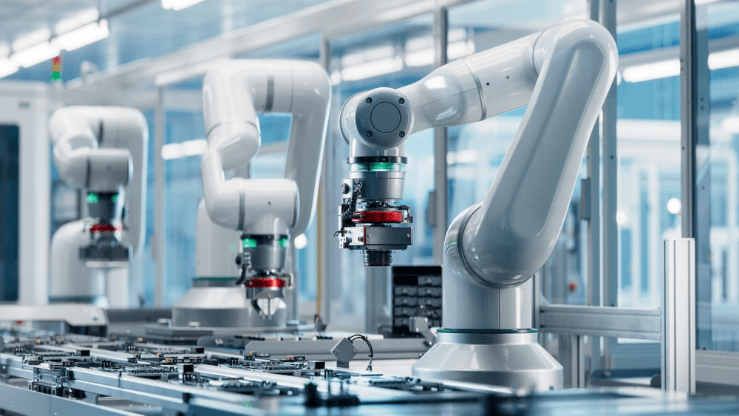
Automated Inspection
Advantages of incorporating artificial intelligence into automated inspection systems include:
• Defect Detection: AI algorithms, particularly machine learning models, are trained to recognize various types of defects that may occur during PCB assembly, such as soldering defects (e.g., solder bridges, insufficient soldering, or solder balls), component misalignment and missing components. These algorithms analyze images captured by inspection cameras to identify and classify defects accurately and rapidly.
• Adaptive Learning: AI models can continuously learn from new data and feedback, allowing them to improve their performance over time. This adaptive learning capability enables AI-powered inspection systems to become more accurate and effective as they are exposed to a greater variety of PCB designs and assembly conditions.
• Real-time Monitoring: AI-powered inspection systems can provide real-time monitoring of the assembly process, continuously analyzing data from inspection cameras to detect defects as they occur. This allows for immediate corrective action to be taken, reducing the likelihood of defective products reaching the end of the production line.
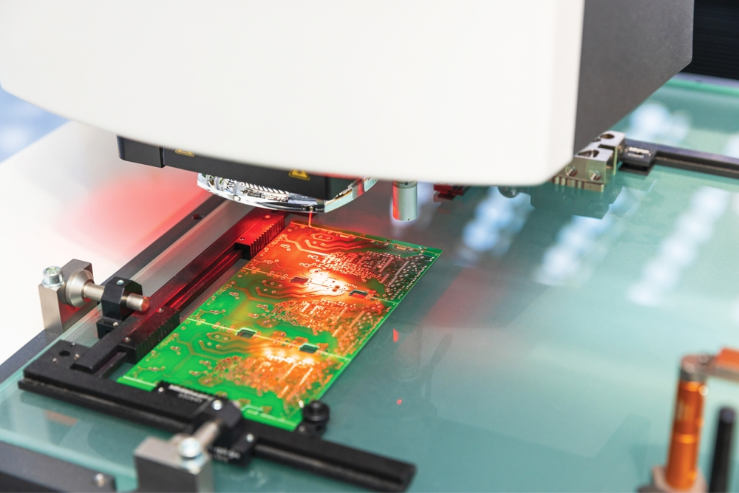
Fault Diagnosis and Rework Assistance
Artificial Intelligence plays a crucial role in fault diagnosis and rework assistance for PCB assembly by leveraging advanced algorithms and machine learning techniques. Here’s how AI is applied in these areas:
Fault Diagnosis:
• Pattern Recognition: AI algorithms recognize patterns in fault data to identify common issues or trends across different printed circuit board assemblies. By analyzing historical fault data, AI can predict potential failure modes or recurring issues and suggest preventive measures to mitigate them.
• Sensor Data Analysis: In addition to visual inspection, AI can analyze sensor data from the assembly process to detect anomalies or deviations from expected parameters. For example, changes in temperature, voltage, or pressure may indicate potential faults or defects in the assembly.
Rework Assistance:
• Guided Repair: AI systems provide guided instructions to operators or technicians for repairing identified faults or defects. By analyzing the nature of the fault and the assembly configuration, AI can recommend the most appropriate rework procedures, such as soldering or component replacement, along with step-by-step instructions.
• Optimized Rework Processes: AI algorithms optimize the rework process by considering factors such as component availability, repair time, and cost-effectiveness. By analyzing historical rework data and performance metrics, AI can suggest the most efficient rework strategies to minimize downtime and maximize productivity.
• Real-time Feedback: AI systems provide real-time feedback during the rework process, ensuring that operators follow the correct procedures and achieve the desired outcome. This includes monitoring soldering quality, component alignment, and overall workmanship to ensure that the reworked printed circuit board meets quality standards.
Conclusion
In conclusion, the integration of artificial intelligence in PCB assembly has brought about transformative changes, revolutionizing efficiency and quality in the electronics manufacturing industry. From predictive maintenance to robotic assembly and automated inspection, AI optimizes processes, enhances productivity, and ensures the delivery of high-quality assembled electronics.
PCB Assembly Express is a full-service electronic contract manufacturer (ECM) located in Tualatin, Oregon. We are constantly investing in the latest SMT and through-hole equipment to guarantee the highest quality in our services, while optimizing costs and delivery times.
LEAVE A REPLY